Cp,Cpkから不良率算出(*・ω・*)b♪ [品質のお話]
今日はついに工程能力指数で求めた値から不良率を算出する方法ですv(。・ω・。)ィェィ♪
工程能力指数のい詳細はこちらを↓↓
http://yu-noppo.blog.so-net.ne.jp/2014-05-18
http://yu-noppo.blog.so-net.ne.jp/2014-05-21
んでそのやり方はというと簡単・・・じゃじゃん(*^ワ^*)
=(1-NORMSDIST(n *3)) * 2 * 100
この式をエクセルで叩いてください。
そして式の中のnを算出した工程能力指数の値を代入。
これで得られた値が不良率です。
注意として、この計算式では、EXCELの%表示の書式にせずに ×100倍をして、直接、不良率(%)を算出しています。
なので書式設定を行って、後ろに「%」をつけたい場合は式の最後の「*100」を外してください。
あと、不良率が小さすぎる場合は、「*100」を「*1000000」(百万)にしてppmを活用してください。(`・ω・´)ノ
さて、皆さんの管理する工程のう不良率の推測値はいかがでしょうか?(´∀`*)ウフフ
--------------------------------------------
目次へ→
-------------------------------------------
工程能力指数と不良率の関係 v(。・ω・。)ィェィ♪ [品質のお話]
さて、今日はついに工程能力指数に関する続きです(*`σェ´*)フムフム
前回は工程能力指数のCpとCpkの違いについてと一般的な判定基準についてお話しました(`・ω・´)ノ
前回の詳細は↓をご覧ください。
http://yu-noppo.blog.so-net.ne.jp/2014-05-18
今回は工程能力指数の値と不良率について書きます(*・ω・*)b♪
以下、代表的なCp,Cpkの値とその不良率です。
-----------------------------------------------------------
〈Cp,Cpk〉〈不良率(%)〉〈不良率(ppm)〉
0.33 31.7% 317311ppm
0.50 13.4% 133614ppm
0.67 4.5% 45500ppm
1.00 0.27% 2700ppm
1.33 0.0063% 63.3ppm
1.50 0.00068% 6.8ppm
ーーーーーーーーーーーーーーーーーーーーーーー
文献によっては「%」ではなく「ppm」で不良率を表しているものもあります(`・ω・´)ノ
ぼくは最初の頃、このppmの意味がわかんなくてだいぶイライラした記憶があります。
なので解説しておきます(*`σェ´*)フムフム
先ずは「%(パーセント)」についてはご存知のとおり百分率というやつですね。
これを違う書き方をすると、「ppc」となります。(こんな書き方は普通しないと思いますが・・・)
もうちょい詳しく書くと、
最初のpは「parts」・・・パーツ、つまり個数のこと
次のpは「per」・・・パー、つまり割り算のこと、/とか÷とかですね?
次のcは「cent」・・・センチ、単位の接頭語でcm(センチメートル)とか身近ですね?百分の一のことです。
つまり「%」とは、ppcやp/cと書くこともでき、個数÷100って意味だってこと(`・ω・´)ノ
そして本題!ppmは「c」が「m」にすげ変わってますよね?この「m」は「million」ミリオンのこと。
要するに100万で割り算する百万分率ってことですv(。・ω・。)ィェィ♪
要は%のより細かい数字を見るときに使う単位です。
ほかにも・・・・
ppb(パーツ・パー・ビリオン)・・・十億分率
ppt(パーツ・パー・トリリオン)・・・一兆分率 なんてものもあるそうです(`・ω・´)ノ
以上、簡単ですが工程能力指数と不良率について&余談でございました(*・ω・*)b♪
さて、じゃあこれ以外の工程能力指数の値が出てきたとき、その不良率をきちんと算出する方法はないの??
ってところが気になってくるかと思います(`・ω・´)ノ
はい!!工程能力指数の値から不良率を算出することは可能です!!!
しかもエクセルの計算式で+。:.゚(*゚Д゚*)キタコレ゚.:。+゚
というわけで次回はココのところを詳しく書いてみたいと思います(`・ω・´)ノ
それでは今日もお付き合いありがとうございました⊂(・∀・)∂))バイバイ
--------------------------------------------
目次へ→
--------------------------------------------
前回は工程能力指数のCpとCpkの違いについてと一般的な判定基準についてお話しました(`・ω・´)ノ
前回の詳細は↓をご覧ください。
http://yu-noppo.blog.so-net.ne.jp/2014-05-18
今回は工程能力指数の値と不良率について書きます(*・ω・*)b♪
以下、代表的なCp,Cpkの値とその不良率です。
-----------------------------------------------------------
〈Cp,Cpk〉〈不良率(%)〉〈不良率(ppm)〉
0.33 31.7% 317311ppm
0.50 13.4% 133614ppm
0.67 4.5% 45500ppm
1.00 0.27% 2700ppm
1.33 0.0063% 63.3ppm
1.50 0.00068% 6.8ppm
ーーーーーーーーーーーーーーーーーーーーーーー
文献によっては「%」ではなく「ppm」で不良率を表しているものもあります(`・ω・´)ノ
ぼくは最初の頃、このppmの意味がわかんなくてだいぶイライラした記憶があります。
なので解説しておきます(*`σェ´*)フムフム
先ずは「%(パーセント)」についてはご存知のとおり百分率というやつですね。
これを違う書き方をすると、「ppc」となります。(こんな書き方は普通しないと思いますが・・・)
もうちょい詳しく書くと、
最初のpは「parts」・・・パーツ、つまり個数のこと
次のpは「per」・・・パー、つまり割り算のこと、/とか÷とかですね?
次のcは「cent」・・・センチ、単位の接頭語でcm(センチメートル)とか身近ですね?百分の一のことです。
つまり「%」とは、ppcやp/cと書くこともでき、個数÷100って意味だってこと(`・ω・´)ノ
そして本題!ppmは「c」が「m」にすげ変わってますよね?この「m」は「million」ミリオンのこと。
要するに100万で割り算する百万分率ってことですv(。・ω・。)ィェィ♪
要は%のより細かい数字を見るときに使う単位です。
ほかにも・・・・
ppb(パーツ・パー・ビリオン)・・・十億分率
ppt(パーツ・パー・トリリオン)・・・一兆分率 なんてものもあるそうです(`・ω・´)ノ
以上、簡単ですが工程能力指数と不良率について&余談でございました(*・ω・*)b♪
さて、じゃあこれ以外の工程能力指数の値が出てきたとき、その不良率をきちんと算出する方法はないの??
ってところが気になってくるかと思います(`・ω・´)ノ
はい!!工程能力指数の値から不良率を算出することは可能です!!!
しかもエクセルの計算式で+。:.゚(*゚Д゚*)キタコレ゚.:。+゚
というわけで次回はココのところを詳しく書いてみたいと思います(`・ω・´)ノ
それでは今日もお付き合いありがとうございました⊂(・∀・)∂))バイバイ
--------------------------------------------
目次へ→
--------------------------------------------
まだ腰痛(´Д` [日記]
だいぶ腰痛も楽になり、歩くの座るのには支障なくなりました( ̄^ ̄)ゞ
でもまだ痛いし、無意識にかばうせいか、職場では歩き方や姿勢がおかしいと指摘されてます^^;
実際まだ座ってても痛いので、今日はスマホから書くことにしました( ̄+ー ̄)
なので、工程能力指数の続きは今日も棚上げしたまんまです(-_-)
申し訳ありませんm(_ _)m
もうどんな風に書くかはだいたい頭の中にあるのであとは、書くだけなんです。
必ず書きますのでもう少し僕の腰に時間をやって下さい。
さて話は腰痛に戻りますけど、一口に腰痛って言ってもその原因と酷さは人それぞれなんですよね?
適当なアンマやさんでスッキリする人もいれば整骨や整体じゃなきゃ治らない人も居ますし、冷やしてマシになる人もいます(・Д・)ノ
僕の場合は、ゆっくりお風呂に使って湯舟でマッサージ後にストレッチ(整体師直伝)でだいぶマシになります。(`_´)ゞ
どうも僕の主治医が言うには、腰は身体を使う動作の中心だから身体のいろんな部位の影響をうける様です(・Д・)ノ
直接的な痛い原因は間違いなく腰付近にあって、痛みの根源はそんないっぱいないんだけど、どうしてそこが悪くなったのか?って要因は肩コリだったり、足の疲れ、日常の姿勢、ストレスや緊張による筋肉の疲労とかいっぱいあるみたいですね( ̄O ̄;)
だから真の治療方は千差万別みたいです。
よくぎっくり腰はクセになるとか言いますが、あれは一回やっちゃうと無意識に警戒して、腰をかばう様になり、その結果何処かが過剰に疲れちゃってうんぬんと言う理由があるみたいです。
てか素人なんで僕なりの主治医の説明をそう解釈したってことで間違ってたらすいませんm(_ _)m
でもそうだとしたら、腰痛あなどりがたしですよね?
僕も最初はそんなひどい腰痛持ちじゃ無かったんですよ?
でも最初の軽いうちをあなどって無理してたらあっと言う間に悪化(T ^ T)
年間に4回、立てなくなるほどになりました´д` ;
痛いを通り越して、もう力が入らないんですよね?
んで治療に通って今は痛くなってもまだ動けるし、おしえられたマッサージやストレッチを3日程頑張れば元通りになります(^_^)☆
実際今回の腰痛は約1年半ぶりですんで、確実にマシにはなってるんです。
今回のは完璧ぼくの油断が原因でしたorz
みなさんもたかだか腰痛と侮らないで下さい。
痛いなぁってのが続く様なら即病院に行って下さい(・Д・)ノ
特に僕みたいな独身男性!!
いい年して母親にズボンはかせて、靴下はかせて!は辛すぎるでしょ?
ちなみに僕の家は祖父母が同居してたこともあり、一部バリアフリーの手すりつきなので、気合いとほふく前進でなんとか、歩けない間の日常生活をクリアしました´д` ;
今は思い出してもあれは2度となりたく無いです(-_-)
ホント、腰には気をつけましょう
腰痛(;´Д`A [日記]
本当は今日、昨日書いた工程能力指数のお話の続きを書きたかったんですが(−_−;)
やってしまいました・・・今朝から腰痛発生です。
何とか出社し、現場のことも含め夕方まで仕事しましたが、明らかに悪化してますorz
pcのまえに座っているのも辛い状況です。激痛を通り越しました。
いつもの僕ならここで自分が腰痛もちになった経緯とかをダラダラ書くんでしょうが今日はもう無理です(´Д` )
せめて明日からはコルセットはめたらまともに動ける程度に復活しててくれる事を祈って、今日は休みます。
みなさん、お身体にはくれぐれもお気をつけ下さい。
工程能力指数(*`σェ´*) [統計学]
さて、今日は工程能力指数についてのお話を少し詳しく(`・ω・´)ノ
品質管理や品質保証をやる人なら耳にしたことある言葉ですよね?
要はその工程の製造精度が規格に対してどの程度の実力を持っているか?という数字.....φ(・ω・*)
CpとCpkがあります(*・ω・*)b♪
まずはどんなものかってイメージが大切ということで・・・
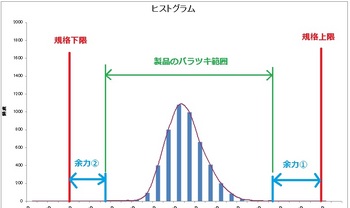
あるデータのヒストグラムです。
ヒストグラムが何なのかについてはこちら↓をご覧ください。
赤線が規格の上限と下限、それに対し緑線が工程のバラツキ範囲。
そして水色線がバラツキ範囲と規格線の隙間・・・つまり余力です(*・ω・*)b♪
当然この隙間が大きいほど不良が発生しにくいということは感覚的にわかることですが、じゃあそこんとこ完全に信用していい隙間の広さってどのくらいなの?このデータからみてこの程度隙間あいてるのは良しとしていいレベルなの??
ってところを数値化したのが工程能力指数です(*・ω・*)b♪
Cpとは規格の幅を製品のバラツキの幅で割り返したものです(`・ω・´)ノ
製品のバラツキの幅は6σ・・・つまり標準偏差の6倍です。
エクセルでの標準偏差の計算式は「=STDEV(セル:セル)」です。
つまりσ=STDEV(セル:セル)を求め、
Cp=(規格上限-規格下限)/(6*σ) という式になります。
ちなみに文献では規格上限を「USL」、下限を「LSL」と表記しているものもあります.....φ(・ω・*)カキカキ
これで得られた値がバラツキから見た隙間の広さを数値化したものです。
数値が大きければ大きいほど優秀ってことですね(`・ω・´)ノ
んでCpはわかったけどCpkって??ってところですが、もう一度このグラフを見てくださいv(。・ω・。)ィェィ♪
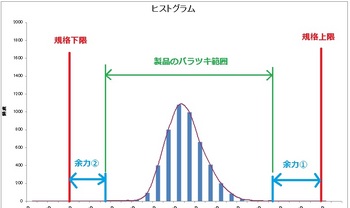
ちょっとわかりにくいですが、青線の余力①と余力②の広さは全く同じでしょうか??
そうです、余力②の方がちょっと狭いんですよね?
製造現場において、製品寸法の平均値が規格の真ん中にどんぴしゃで重なっていることなんてまずありえなくて、常に上限か下限のどちらかにわずかでもシフトしているはず(`・ω・´)ノ
Cpの計算は単に規格の広さ÷バラツキ範囲の広さという計算をしているだけでこのことを全く加味していないんですΣ(°□°)⊃------マジッ
Cpkはこれを加味しているんですね。
計算式は・・・
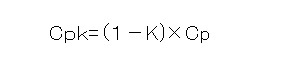
ここで出てくる「K」は偏り係数・・・つまり規格の真ん中から平均値がずれていることを前提にそのズレを算出する値です( ̄Д ̄)ノ
そのKをまず算出する必要があるので計算式を・・・

・・・はい、意味わかりません(´∀`*)ウフフ
僕中学校以降、大学まで一番嫌いな科目は数学でした☆
なのでこんな式意味わかりません状態でした。こんな計算式クソ食らえです(*^ワ^*)
でも必要なことだから必死に解こうとしてたんですがね、調べて句とエクセルでこれを簡単に算出する方法を知りましたv(。・ω・。)ィェィ♪
それがこちら↓

ここで出てくる「μ」という記号は平均値のことです。
なのであらかじめ、平均を算出しておきましょう。エクセルでの計算式は「=AVERAGE(セル:セル)」ですね(`・ω・´)ノ
んで上の公式の=から右側をμのところだけ平均値に変えてそのまま入力してもらえればCpkが算出されます(*・ω・*)b♪
ちなみに「=Min( , )」もエクセルの計算式のひとつ。
なにを計算しているかというと・・・
1、、、(規格上限-平均値)/(3*σ)
2、、、(平均値-規格下限)/(3*σ)
を求めて1と2のより小さい方・・・つまり上下それぞれの規格線に対し、より小さい隙間がどっちかを見て算出しているんです。
σに掛ける数値が6じゃなくて3なのも、バラツキの平均値を中心にそれぞれ規格上限までと規格下限までの距離を別々に見に行ってるから・・・全体だと6σ、半分だと3σって話ですね(*`σェ´*)フムフム
さてこんな感じでCpkってのは現実としてデータの平均値は規格の中心とイコールではないという前提で真の実力を見に行ってる数値ということです(`・ω・´)ノ
じゃあCpってあんまり使えない数値なんだね( ̄Д ̄)ノ
ってお話ではありませんよ?CpもCpkもどちらも大切です。
まぁ簡単にいうと
Cpkというのは加工狙い値などのチューニング誤差まで含んだ現実的な実力値(`・ω・´)ノ
Cpというのは仮に加工狙い値と規格中心が重なるまでチューニングすればここまでの実力を発揮できるという値(*・ω・*)b♪
だと僕は解釈しています(*`σェ´*)フムフム
つまり、まずCpをみて工程能力指数が根本的に足りるかどうかを判断!
ここで足りなきゃ即改善!足りてりゃCpkを見る!!
Cpkだけが足りないならチューニングだけで何とかなるかも知れないってことですv(。・ω・。)ィェィ♪
ちなみに工程能力指数がいくらだったらどうなのってお話ですがその判断基準は一般的に・・・
Cp(またはCpk)≧1.67・・・十分すぎる能力。
バラツキが多少大きくなっても心配なく、
管理の簡素化を検討してもよいレベル。
1.67>Cp(Cpk)≧1.33・・・十分な能力。
この状態を維持するべき。
1.33>Cp(Cpk)≧1.00・・・十分とはいえないがまずまず。
1.00に近づくと不良発生の可能性があるので、
しっかり管理し、必要に応じて処置する。
1.00>Cp(Cpk)≧0.67・・・能力不足。
不良品が発生していることが予想される。
全数検査による製品の選別と改善処置が必要。
0.67>Cp(Cpk)・・・・・・・・工程能力が非常に不足している。
品質を満足できる状態ではなく、原因の究明と改善対策を
緊急的に行う必要がある。
または規格の再検討を行う。
ということです(*`σェ´*)フムフム
さて、普段抜取検査だけで管理している工程はありませんか?
一度n数を集めてCp・Cpkを算出されてはいかがでしょうか?
PS
工程能力指数もデータが正規分布に帰属することを前提としています(`・ω・´)ノ
なのでヒストグラムや歪度や尖度の確認もしっかり行ってください。
それでは本日もお付き合いいただきありがとうございました⊂(・∀・)∂))バイバイ
------------------------------------
目次へ→
------------------------------------
品質管理や品質保証をやる人なら耳にしたことある言葉ですよね?
要はその工程の製造精度が規格に対してどの程度の実力を持っているか?という数字.....φ(・ω・*)
CpとCpkがあります(*・ω・*)b♪
まずはどんなものかってイメージが大切ということで・・・
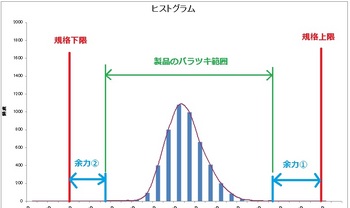
あるデータのヒストグラムです。
ヒストグラムが何なのかについてはこちら↓をご覧ください。
赤線が規格の上限と下限、それに対し緑線が工程のバラツキ範囲。
そして水色線がバラツキ範囲と規格線の隙間・・・つまり余力です(*・ω・*)b♪
当然この隙間が大きいほど不良が発生しにくいということは感覚的にわかることですが、じゃあそこんとこ完全に信用していい隙間の広さってどのくらいなの?このデータからみてこの程度隙間あいてるのは良しとしていいレベルなの??
ってところを数値化したのが工程能力指数です(*・ω・*)b♪
Cpとは規格の幅を製品のバラツキの幅で割り返したものです(`・ω・´)ノ
製品のバラツキの幅は6σ・・・つまり標準偏差の6倍です。
エクセルでの標準偏差の計算式は「=STDEV(セル:セル)」です。
つまりσ=STDEV(セル:セル)を求め、
Cp=(規格上限-規格下限)/(6*σ) という式になります。
ちなみに文献では規格上限を「USL」、下限を「LSL」と表記しているものもあります.....φ(・ω・*)カキカキ
これで得られた値がバラツキから見た隙間の広さを数値化したものです。
数値が大きければ大きいほど優秀ってことですね(`・ω・´)ノ
んでCpはわかったけどCpkって??ってところですが、もう一度このグラフを見てくださいv(。・ω・。)ィェィ♪
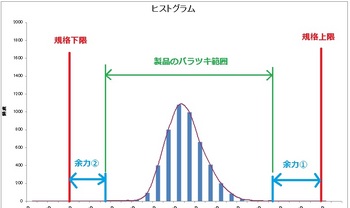
ちょっとわかりにくいですが、青線の余力①と余力②の広さは全く同じでしょうか??
そうです、余力②の方がちょっと狭いんですよね?
製造現場において、製品寸法の平均値が規格の真ん中にどんぴしゃで重なっていることなんてまずありえなくて、常に上限か下限のどちらかにわずかでもシフトしているはず(`・ω・´)ノ
Cpの計算は単に規格の広さ÷バラツキ範囲の広さという計算をしているだけでこのことを全く加味していないんですΣ(°□°)⊃------マジッ
Cpkはこれを加味しているんですね。
計算式は・・・
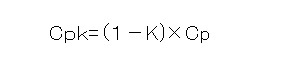
ここで出てくる「K」は偏り係数・・・つまり規格の真ん中から平均値がずれていることを前提にそのズレを算出する値です( ̄Д ̄)ノ
そのKをまず算出する必要があるので計算式を・・・

・・・はい、意味わかりません(´∀`*)ウフフ
僕中学校以降、大学まで一番嫌いな科目は数学でした☆
なのでこんな式意味わかりません状態でした。こんな計算式クソ食らえです(*^ワ^*)
でも必要なことだから必死に解こうとしてたんですがね、調べて句とエクセルでこれを簡単に算出する方法を知りましたv(。・ω・。)ィェィ♪
それがこちら↓

ここで出てくる「μ」という記号は平均値のことです。
なのであらかじめ、平均を算出しておきましょう。エクセルでの計算式は「=AVERAGE(セル:セル)」ですね(`・ω・´)ノ
んで上の公式の=から右側をμのところだけ平均値に変えてそのまま入力してもらえればCpkが算出されます(*・ω・*)b♪
ちなみに「=Min( , )」もエクセルの計算式のひとつ。
なにを計算しているかというと・・・
1、、、(規格上限-平均値)/(3*σ)
2、、、(平均値-規格下限)/(3*σ)
を求めて1と2のより小さい方・・・つまり上下それぞれの規格線に対し、より小さい隙間がどっちかを見て算出しているんです。
σに掛ける数値が6じゃなくて3なのも、バラツキの平均値を中心にそれぞれ規格上限までと規格下限までの距離を別々に見に行ってるから・・・全体だと6σ、半分だと3σって話ですね(*`σェ´*)フムフム
さてこんな感じでCpkってのは現実としてデータの平均値は規格の中心とイコールではないという前提で真の実力を見に行ってる数値ということです(`・ω・´)ノ
じゃあCpってあんまり使えない数値なんだね( ̄Д ̄)ノ
ってお話ではありませんよ?CpもCpkもどちらも大切です。
まぁ簡単にいうと
Cpkというのは加工狙い値などのチューニング誤差まで含んだ現実的な実力値(`・ω・´)ノ
Cpというのは仮に加工狙い値と規格中心が重なるまでチューニングすればここまでの実力を発揮できるという値(*・ω・*)b♪
だと僕は解釈しています(*`σェ´*)フムフム
つまり、まずCpをみて工程能力指数が根本的に足りるかどうかを判断!
ここで足りなきゃ即改善!足りてりゃCpkを見る!!
Cpkだけが足りないならチューニングだけで何とかなるかも知れないってことですv(。・ω・。)ィェィ♪
ちなみに工程能力指数がいくらだったらどうなのってお話ですがその判断基準は一般的に・・・
Cp(またはCpk)≧1.67・・・十分すぎる能力。
バラツキが多少大きくなっても心配なく、
管理の簡素化を検討してもよいレベル。
1.67>Cp(Cpk)≧1.33・・・十分な能力。
この状態を維持するべき。
1.33>Cp(Cpk)≧1.00・・・十分とはいえないがまずまず。
1.00に近づくと不良発生の可能性があるので、
しっかり管理し、必要に応じて処置する。
1.00>Cp(Cpk)≧0.67・・・能力不足。
不良品が発生していることが予想される。
全数検査による製品の選別と改善処置が必要。
0.67>Cp(Cpk)・・・・・・・・工程能力が非常に不足している。
品質を満足できる状態ではなく、原因の究明と改善対策を
緊急的に行う必要がある。
または規格の再検討を行う。
ということです(*`σェ´*)フムフム
さて、普段抜取検査だけで管理している工程はありませんか?
一度n数を集めてCp・Cpkを算出されてはいかがでしょうか?
PS
工程能力指数もデータが正規分布に帰属することを前提としています(`・ω・´)ノ
なのでヒストグラムや歪度や尖度の確認もしっかり行ってください。
それでは本日もお付き合いいただきありがとうございました⊂(・∀・)∂))バイバイ
------------------------------------
目次へ→
------------------------------------
現場の基本(*`σェ´*) [お仕事関連のお話]
いやぁ僕もぶっちゃけ苦手なんですがね、製造現場の最も基本的な事3S、5Sというのがあります(`・ω・´)ノ
まぁホント良く耳にする話でこんな常識的なことを今更って感じですが書きます(*・ω・*)b♪
自己満足的に書きます(。・Д・)ゞ
3Sとは
整理(seiri)・・・必要なものと不要なものをしっかり分けて不要なものを買わない、置かない
整頓(seiton)・・・整理して残ったものを合理的に配置し、誰でもわかる様にする。(明示など)
清掃(seisou)・・・掃除道具などを使い清々しくきれいな状態にする。
これらの頭文字が全てSだから3Sってわけですね(`・ω・´)ノ
じゃあ5Sってなによ?ってなると3Sに
清潔(seiketu)・・・3Sの状態を維持し続けること
躾(situke)・・・決められたことをいつも正しく守ること。
躾(しつけ)が習慣化(だれもが日常的に5Sを実施するよう習慣づけること)と書かれている文献もありますね(`・ω・´)ノ
んでここに
セーフティ(safety)・・・安心して作業を任せられ、安全な現場をつくること
が加わり6Sになる場合もあります(*`σェ´*)フムフム
さて、つらつらと偉そうにこんな教科書の文言を並べてみましたが、実際3Sも5Sも6Sもとっても重要です!でもこんな文言を覚えることに価値はなかったりします(`・ω・´)ノ
考えてみて下さい。
現場に不要なものとかが雑多に置かれており、作業する人が必要な道具や書類がどこにあるかわからない状況で生産活動は効率的におこなえますか?
現場がホコリだらけで普通にゴミなんかが落ちてる状況でキレイな製品はできますか?
出荷前の段階でホコリや異物が付着してて、それでも気にしない企業をお客さんは気持ちよく信頼してくれますか??
3S必要ですよね(*・ω・*)b♪
何人かの社員で整理整頓を一生懸命やったあとから別の社員が散らかして行くの会社として放っておいていい状況でしょうか?
そしたらまた他の人が整理整頓に手を取られて時間のムダでしかないですよね??
いくら現場の効率が上がり生産性が良くなった所で従業員がけがしたり事故を起こす様な現場では論外ですよね?
つまり、会社としての不合理なことや最低限やらなければ行けないことを考えて行けば、整理整頓だの
なんだのは必然的にやるべきことに入ってくるんです(`・ω・´)ノ
大切なのは3Sだの5Sだの言うことではなく、従業員がそういう目線で自分の働く現場を見ることができているかどうかなんです(*`σェ´*)
ただ見た目をキレイにするだけじゃない、合理的か?品質・効率に影響はないか?誰でもわかるか?お客さんが来た時に不快感を感じないか?そういう目線でこそ3S、5S活動は行うべきだと思います(p゚д゚q)
-----------------------------------
目次へ→
----------------------------------
自分の値段(・Д・)ノ [お仕事関連のお話]
昨日はサラリーマンとは自分の能力と時間を売って収益を得るもんだという話でした(・Д・)ノ
そういう話になったのも理由がありまして、今日はうちの会社での管理職の値段が決定される日だったんです( ̄^ ̄)ゞ
要は面接シート(自分の値札)を出して社長とのこの1年こんな事をやってこれだけ稼いだからいくらの給料を下さいよって話をするんですね(`_´)ゞ
これがうちの会社のいいとこ悪いとこです(・Д・)ノ
自分の給料を直接社長と交渉できるから昇給額がちいさくてもそれは自分のせいでしかないんですよね?(・Д・)ノ
でも交渉事が苦手な人はいくら実績を上げても面接の中で社長からの信頼をえれなければ昇給しないんですよねぇ(−_−;)
でもね、実績あげても交渉だめなら評価されないなんて辛い話ですけどやっぱ現実です(・Д・)ノ
そういうのをちゃんと念頭におけば、現実的な納得できるシステムだと思います。
後は経営者が公平な判断さえしてればこんな実力社会はないでしょ?
んなこんなで、今年も僕は自分の値段を主張して交渉しまして、その結果社長からの値切りをくらって折れちゃったわけなんですが、それも含めて自分の実力(−_−;)
まぁしゃーないですね。
さぁまた来年までがんばろ(・Д・)ノ
そういう話になったのも理由がありまして、今日はうちの会社での管理職の値段が決定される日だったんです( ̄^ ̄)ゞ
要は面接シート(自分の値札)を出して社長とのこの1年こんな事をやってこれだけ稼いだからいくらの給料を下さいよって話をするんですね(`_´)ゞ
これがうちの会社のいいとこ悪いとこです(・Д・)ノ
自分の給料を直接社長と交渉できるから昇給額がちいさくてもそれは自分のせいでしかないんですよね?(・Д・)ノ
でも交渉事が苦手な人はいくら実績を上げても面接の中で社長からの信頼をえれなければ昇給しないんですよねぇ(−_−;)
でもね、実績あげても交渉だめなら評価されないなんて辛い話ですけどやっぱ現実です(・Д・)ノ
そういうのをちゃんと念頭におけば、現実的な納得できるシステムだと思います。
後は経営者が公平な判断さえしてればこんな実力社会はないでしょ?
んなこんなで、今年も僕は自分の値段を主張して交渉しまして、その結果社長からの値切りをくらって折れちゃったわけなんですが、それも含めて自分の実力(−_−;)
まぁしゃーないですね。
さぁまた来年までがんばろ(・Д・)ノ
サラリーマンとは(*・ω・*)b♪ [お仕事関連のお話]
今日、元部下の人(歳上)と仕事の後30分くらい雑談してました(`・ω・´)ノ
その時に給料の事とか今後のどうすれば昇給できるのかとかそんな話をしたんですがね、
みなさん自営業で商売をしてると思ってください(*`σェ´*)
その時に商品を売ろうとしてて、その商品は一般の市場に無いものです。
もちろん相場ってものが良くわかんないからお客さんは値段が正当なのか気になる所!
当然値切ってくるお客も居ます(*・ω・*)b♪
そんな時、少しでも儲けたければ如何に自分の商品が良いものなのか?なんでこんな値段設定なのかとか一生懸命説明するでしょう?
それと同じです(*・ω・*)b♪
結局サラリーマンも自営と一緒!!ただ売る商品が物ではなく、「自分の能力と時間」なんです(*`σェ´*)フムフム
だから給料を上げたければ、会社にとっての「自分の価値」を上げることを考えなきゃいけないし、それをきちんと上司や経営者に伝えなきゃいけないんです(`・ω・´)ノ
上司や経営者の責任は少しでも支出を抑え、会社の収入を増やす方法を考えること!
ホントは収入を増やすのはみんなで分けるお金を増やすためであって欲しいんですが、不景気のお陰で最近の経営者は少しでも会社にお金を残す方に思考が行きがちです。
特に中小企業は!!(;´Д`)
でもね、そんな経営者も良くないけどそれをただ批判してても前には進みません(`・ω・´)ノ
仮に買い物しててね、前行った店で1万円だった商品があったとして、それは自分の思う相場からみて納得の値段だったけど次の店では5千円でした!
わざわざ「前の店だと1万円だったし僕もそれぐらいだと思うから〜♪」って1万円出します???
大喜びで「ラッキ〜☆」っていいながら5千円で買うでしょ??
同じ話です!
雇われている人が自分の価値が以前と同じで無いことをきちんと投げかけないと自分の思う値段に近づけることなんて無いと思わなきゃダメなんです(。・Д・)ゞ
ホントはそんな仕組み間違ってると思います(*・ω・*)b♪
経営者は従業員にやる気になってもらうために率先して昇給を提唱して欲しいです。
でもねそんな企業も確かにあるけどいっぱいあるかな?それが一般的に普通と言う社会かな??
違うんですよね今の世の中・・・でもそんな嫌な仕組みでも僕らの前にある現実です( p′︵‵。)
仮にきちんとアピールしてるし、それは実績や根拠のある自分の価値を正しく訴えているのに、しかも会社は潤っているのに認めてもらえないなんてこともあるでしょう。
それもさっきの自営の例で考えて下さい(`・ω・´)ノ
自分の説明を聞き入れてもらえず、ひたすら値切ってくる!
この人に売った所で宣伝してくれるとか、他のお客を紹介してくれるなんてメリットもない。
この人の言い値で売ったら赤字だ!ってときどうします??
売らないでしょ?
そう!そんな経営者に自分の能力と時間を売らなきゃいいんです(*・ω・*)b♪
要は転職すべきって事ですね。
これも楽じゃないけど、そんだけ能力のある人ならそういう努力もすべきだと思います。
とにかく、ただ毎日を過ごし、自分を高めようとせず惰性で日々仕事をしているんじゃダメです(`・ω・´)ノ
同じ仕事を毎日してたらそりゃ慣れますから一年後には去年より要領も良くなるでしょう!
そこは評価・昇給に値します!でも10年続けた同じ仕事をやってて11年目はさらに要領よくなる?
惰性でやってたらそこはもう成長しなくなっちゃいますよね?
そんなんだと昇給なんてしなくて当たり前!!
まぁ会社が大きく成長してるならそれもありでしょうけど、それでも日々切磋琢磨してる人と同じだけ昇給してたらある意味それも正当な評価をやってる会社じゃないですよね?(;´Д`)
うちの会社も今不景気です(`・ω・´)ノ
でもなんとか持ち直して、貢献してくれた人にはきちんと見合った報酬や昇給を行える様、なんとか業績を回復したいものです(*`σェ´*)フムフム
今日も良くわからんとりとめのない文章で失礼しました⊂(・∀・)∂))バイバイ
-----------------------------------------
目次へ→
-----------------------------------------
続・4M [品質のお話]
さてこの間書いた4Mのお話の続編です(`・ω・´)ノ
前回は4M変更管理を侮ると痛い目にあいますよってお話を書きました。
じゃあ何がどうして重要なの?って所を今日語ります。
前の記事を読まれていない方はこちら↓をどうぞ
http://yu-noppo.blog.so-net.ne.jp/2014-05-11
先ずね製造業において、品質ってなぜ保たれていると思います?
これはずいぶん前にも書きましたが、突き詰めて行くと「偶然」なんですΣ(°□°)⊃------マジッ
具体的に言えば、、、
例えば金属の表面をある設備で研磨加工しようとしたとします。
要求品質は研磨された後の表面荒さとしましょう(`・ω・´)ノ
きっと品質に絡む主な要素はざっと考えても
砥石の荒さ、砥石の外径(接触面にかかるトルクに影響)、回転速度、モータのトルク、加工前の材料の状況、環境温度による材料の膨張度合い、研磨時間、砥石の食い込み量とか色々出てきますよね?
この作業が一日100回、1000回と繰り返されるとして、毎回全く同じ、つまりバラツキ0のパラメータっていくつあります??
例えば新品の砥石に対し、軽い力で何度か使用された砥石・その前に柔らかいものを削った砥石には多少の目詰まりが起きていて、研磨する力が変りますよね?
食い込み量を滑りねじとモータで制御したとして、がたつき0の滑りねじなんて滑りませんよね?
研磨時間をアナログの制御用タイマーで管理してたとしましょう。その繰り返し精度は?
砥石の外形が大きい時と小さい時って研磨面にかかる力は変るでしょ?
気温が高いと金属は膨張するから実質の食い込み量は変りますよね?
ぱっと考えるだけでもこんなに考えなきゃ行けないことがあります(`・ω・´)ノ
ばらつく要素はホントたくさんあります。でも全く同じものを作れる条件ってのは非常に狭いふれ幅しか許されませんよね?
今既に自分の現場で量産され、品質的にも合格している製品を思い出して下さい。
その製造を行う時、管理されているパラメータっていくつあります?
そして今度は管理されていない中で極端に変えたら影響でるな?って想像つきそうなものを考えて下さい。たぶん「そんなもん見つからない」ってことはないと思います(`・ω・´)ノ
そしてここから重要!!
僕らが今働いている現場は、先輩たちが長い時間をかけてひとつずつこういうことをクリアし、品質を安定させてきて、心配しなきゃ行けないこと、考えなきゃいけない事を減らして来たんです(*・ω・*)b♪
例えば、膨張収縮を少しでも抑える為に空調を入れて室温を均等に保ってました(`・ω・´)ノ
その温度は23℃の設定!それに対して節電だーって言って28℃に設定を上げる様ルール変更しました。
これ確実に材料の膨張収縮の条件変ってますよね?
それが品質に影響ないかどうかはその材料の事をきちんと知っている専門のスタッフがしっかり考えるか、実際にその環境でテストするかしないとわかりませんよね?
それをせずに結果的に品質異常はありませんでした!なんて話はホントに偶然通りこして運がよかっただけの話になっちゃいますよね?
そう僕らが普段何気なしにやっている行動だったり、当たり前の環境、使っている設備のメーカーから部品の仕様に至るまで、色んな所に開発者や先輩方、またはどっかの学者さんのそういった思考錯誤がつまっているんです(`・ω・´)ノ
そしてそれらを全て教わり、理解し、ずっと記憶に止めるというのは簡単なことじゃありません。
なので4M変更管理というのが重要になってくるのです(*・ω・*)b♪
例えばさっき上げた空調の話なんかは一見4MのMの中にはパッと該当しませんが、要は4Mとは「人」、「機械」、「材料」、「方法」が変るから影響ないか調べなさいという話ではなくて、現場における何かを変更する場合、それが品質や効率に影響するファクターでないかを検討・検証し影響ある場合は、許容範囲か?影響をいい方に持って行く又は、影響を無くす別の方法は無いかを十分確認しなさいという事だと解釈すべきなんです(`・ω・´)ノ
じゃあルール変更する度に全部実験や検証しないと進んじゃいけないの?
そんなことしてたら、改善一個にしても中々すすみませんよね?だから論理的な思考を身につけること、自らのつくる製品、材料について十分な知識を持ち理論上問題ないと結論付け、それが社内やお客さんに十分納得してもらえる場合は、実験・検証をパスできる場合もあります。
でもそうじゃ無いなら、実験・検証は必須。
そしてその結果を少しでも早くなっとくしてもらおうと思うのなら統計的なデータに基づく説明が必要。それが出来ないなら、5Lot、10Lot、時には3ヶ月や一年の全数検査などの結果を持って承認を得ると言うことさえ必要になります。
どれが一番楽ですか?当然論理的に考えることでしょ??
もし4M管理をせずクレームに至ってしまったら?
お客さんは元に戻せというばかりか、今後いかなる変更も厳しいチェックが入って来たり、全数検査の義務化を要求してきたりするでしょう(;´Д`)
4M・・・あなどりがたしです・・・
----------------------------------
目次へ→
---------------------------------
前回は4M変更管理を侮ると痛い目にあいますよってお話を書きました。
じゃあ何がどうして重要なの?って所を今日語ります。
前の記事を読まれていない方はこちら↓をどうぞ
http://yu-noppo.blog.so-net.ne.jp/2014-05-11
先ずね製造業において、品質ってなぜ保たれていると思います?
これはずいぶん前にも書きましたが、突き詰めて行くと「偶然」なんですΣ(°□°)⊃------マジッ
具体的に言えば、、、
例えば金属の表面をある設備で研磨加工しようとしたとします。
要求品質は研磨された後の表面荒さとしましょう(`・ω・´)ノ
きっと品質に絡む主な要素はざっと考えても
砥石の荒さ、砥石の外径(接触面にかかるトルクに影響)、回転速度、モータのトルク、加工前の材料の状況、環境温度による材料の膨張度合い、研磨時間、砥石の食い込み量とか色々出てきますよね?
この作業が一日100回、1000回と繰り返されるとして、毎回全く同じ、つまりバラツキ0のパラメータっていくつあります??
例えば新品の砥石に対し、軽い力で何度か使用された砥石・その前に柔らかいものを削った砥石には多少の目詰まりが起きていて、研磨する力が変りますよね?
食い込み量を滑りねじとモータで制御したとして、がたつき0の滑りねじなんて滑りませんよね?
研磨時間をアナログの制御用タイマーで管理してたとしましょう。その繰り返し精度は?
砥石の外形が大きい時と小さい時って研磨面にかかる力は変るでしょ?
気温が高いと金属は膨張するから実質の食い込み量は変りますよね?
ぱっと考えるだけでもこんなに考えなきゃ行けないことがあります(`・ω・´)ノ
ばらつく要素はホントたくさんあります。でも全く同じものを作れる条件ってのは非常に狭いふれ幅しか許されませんよね?
今既に自分の現場で量産され、品質的にも合格している製品を思い出して下さい。
その製造を行う時、管理されているパラメータっていくつあります?
そして今度は管理されていない中で極端に変えたら影響でるな?って想像つきそうなものを考えて下さい。たぶん「そんなもん見つからない」ってことはないと思います(`・ω・´)ノ
そしてここから重要!!
僕らが今働いている現場は、先輩たちが長い時間をかけてひとつずつこういうことをクリアし、品質を安定させてきて、心配しなきゃ行けないこと、考えなきゃいけない事を減らして来たんです(*・ω・*)b♪
例えば、膨張収縮を少しでも抑える為に空調を入れて室温を均等に保ってました(`・ω・´)ノ
その温度は23℃の設定!それに対して節電だーって言って28℃に設定を上げる様ルール変更しました。
これ確実に材料の膨張収縮の条件変ってますよね?
それが品質に影響ないかどうかはその材料の事をきちんと知っている専門のスタッフがしっかり考えるか、実際にその環境でテストするかしないとわかりませんよね?
それをせずに結果的に品質異常はありませんでした!なんて話はホントに偶然通りこして運がよかっただけの話になっちゃいますよね?
そう僕らが普段何気なしにやっている行動だったり、当たり前の環境、使っている設備のメーカーから部品の仕様に至るまで、色んな所に開発者や先輩方、またはどっかの学者さんのそういった思考錯誤がつまっているんです(`・ω・´)ノ
そしてそれらを全て教わり、理解し、ずっと記憶に止めるというのは簡単なことじゃありません。
なので4M変更管理というのが重要になってくるのです(*・ω・*)b♪
例えばさっき上げた空調の話なんかは一見4MのMの中にはパッと該当しませんが、要は4Mとは「人」、「機械」、「材料」、「方法」が変るから影響ないか調べなさいという話ではなくて、現場における何かを変更する場合、それが品質や効率に影響するファクターでないかを検討・検証し影響ある場合は、許容範囲か?影響をいい方に持って行く又は、影響を無くす別の方法は無いかを十分確認しなさいという事だと解釈すべきなんです(`・ω・´)ノ
じゃあルール変更する度に全部実験や検証しないと進んじゃいけないの?
そんなことしてたら、改善一個にしても中々すすみませんよね?だから論理的な思考を身につけること、自らのつくる製品、材料について十分な知識を持ち理論上問題ないと結論付け、それが社内やお客さんに十分納得してもらえる場合は、実験・検証をパスできる場合もあります。
でもそうじゃ無いなら、実験・検証は必須。
そしてその結果を少しでも早くなっとくしてもらおうと思うのなら統計的なデータに基づく説明が必要。それが出来ないなら、5Lot、10Lot、時には3ヶ月や一年の全数検査などの結果を持って承認を得ると言うことさえ必要になります。
どれが一番楽ですか?当然論理的に考えることでしょ??
もし4M管理をせずクレームに至ってしまったら?
お客さんは元に戻せというばかりか、今後いかなる変更も厳しいチェックが入って来たり、全数検査の義務化を要求してきたりするでしょう(;´Д`)
4M・・・あなどりがたしです・・・
----------------------------------
目次へ→
---------------------------------
クラタスΣ( ̄□ ̄;) [日記]
結構前から話題にはなってましたけど、クラタス・・・すごいっすねΣ(°□°)⊃------マジッ
水道橋重工の倉田さんがが制作、クラタさんが作ったからクラタス??
既に完成し発売されている様です。
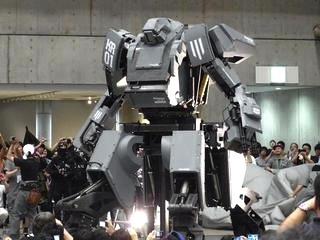
その重量はなんと4tでお値段は135万ドル・・・1億4000万円Σ( ̄□ ̄;)
値段もさるものながらこんな物が出来てしまうってのが日本の技術マジで半端ねぇ(´∀`@)♪
俺もつくりてぇ!!でもそんな技術ねぇ!!( p′︵‵。)
どうもこのクラタス、人が乗って良し、操縦桿握って良し、自分の体を実際動かして操ることもしまいにゃスマホでの遠隔操作まで可!ときてます(`・ω・´)ノ
しかも倉田さん、どっかからのオーダーとかじゃなく作りたいから作ったとかΣ( ̄□ ̄;)
気合いやベーよ! 日本の技術云々もあるけど倉田さんの気合いがスゲーっす(;´Д`)
こちらは制作途中かな?
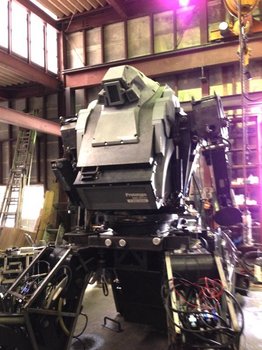
移動は車輪走行の様です(*`σェ´*)
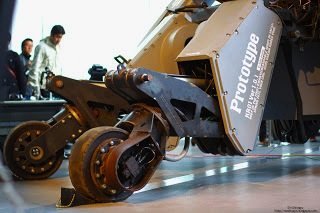
いやマジ本気だね!この人達!きっと途方もない努力と苦労を重ねたんでしょうね(`・ω・´)ノ
そんなかで今ある技術を駆使して、足りない所は新たな技術開発とかもしたんだろうな〜。
どうしても出来ない所なんかはあの手この手で方法を変え、思考を変えて実現したんでしょうねきっと(p゚д゚q)
ホント・・・ただただすごいです。
間違いなく日本のロボット技術は世界一です!!
いつだか、どっかの政治家さんが制作中のスパコンの予算削減するために「なんで世界一を目指さなきゃいけないの?」とか言ってましたよね?
なんでもクソもないでしょっ!資源も軍事力も持たない島国の日本が、他国が戦争やなんやで経済成長を促す中、どうやって成長して来たと思ってるの?何を武器にこの国は生き残って来たの??
技術力でしょうよ!!そして一時はアメリカと並んで先進国のトップに君臨したはいいが成長しすぎた経済は他国との物価の格差を生み、圧倒的に高い人件費と内需だけでは経済が回らないと言うアンバランスな結果に・・・
この先どうやって日本は成長していくの?どうやって経済立て直すの??
資源は無い。土地は狭く山や谷ばっかで農業もやりにくい!!
何を売るの??技術でしょう!!!
阿部さんが今後の日本はロボット産業に革命を起こして経済をうんぬんと宣言していましたが、このクラタスもきっとその一翼を担うんでしょうね(`・ω・´)ノ
まだまだこの先楽しみですね(´∀`@)♪